Istotność badań elementów złącznych mocowań PV
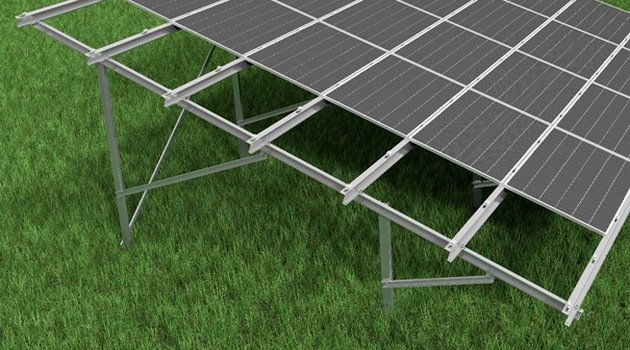
Obecnie na rynku spotykamy się z praktyką, w której producenci i dystrybutorzy kupują i kompletują elementy podkonstrukcji od wielu dostawców, nie dokonując przy tym badań wszystkich złączonych elementów. Takie podejście budzi wątpliwości, czy montowana podkonstrukcja jest trwała i bezpieczna.
Niewłaściwie zamontowana instalacja, zarówno naziemna jak i dachowa, może ulec zniszczeniu na skutek silnego wiatru czy obciążenia od śniegu. Uwolnienie modułów stanowi poważne zagrożenie dla przypadkowych przechodniów i często prowadzi do uszkodzenia innych elementów budynków czy też pojazdów pod nimi zaparkowanych.
Każdy uczestnik inwestycji fotowoltaicznej (Inwestor, Instalator oraz Projektant), niezależnie od skali budowy elektrowni słonecznej oraz etapu planowania realizacji elektrowni słonecznej, powinien zadbać o spełnienie podstawowych wymogów związanych z Ustawą o Wyrobach Budowlanych oraz Prawem Budowlanym. Wykonawca inwestycji już na etapie projektu powinien określić podstawowe wymagania w zakresie zastosowanych materiałów – tzw. poziom właściwości użytkowych wyrobów budowlanych.
Wybór docelowych elementów powinien być uwarunkowany spełnieniem wymogów prawnych oraz dopuszczeniem elementów do obrotu i stosowania ich zgodnie z przepisami ustawy o wyrobach budowanych.
Należy zwrócić uwagę, że zgodnie z Rozporządzeniem Parlamentu Europejskiego i Rady (UE) nr 305/2011 „wyrób budowlany” oznacza każdy wyrób lub zestaw wyprodukowany i wprowadzony do obrotu w celu trwałego wbudowania w obiektach budowlanych lub ich częściach, którego właściwości wpływają na właściwości użytkowe obiektów budowlanych w stosunku do podstawowych wymagań dotyczących obiektów budowlanych.
„Zestaw” oznacza wyrób budowlany wprowadzony do obrotu przez jednego producenta jako zestaw co najmniej dwóch odrębnych składników, które muszą zostać połączone, aby mogły zostać włączone w obiektach budowlanych – budynki i budowle. Oznacza to, że składanie podkonstrukcji z kilku elementów, zakupionych od różnych dostawców, nieprzebadanych łącznie, jest niedopuszczalne.
Aby zapewnić należyte bezpieczeństwo konstrukcji, Energy5 tworzy gotowe systemy mocowań modułów fotowoltaicznych, dokonując badań wszystkich elementów złącznych, prób nośności od obciążeń normatywnych wywołanych wiatrem i śniegiem oraz trwałości korozyjnej zestawu.
Bezpieczeństwo systemów potwierdzają m.in. badania wytrzymałości systemów w tunelu aerodynamicznym oraz porównawcze badania ogniowe systemów zamocowań elewacji wentylowanej, przeprowadzone we współpracy z AGS Sp. z o.o. w Instytucie Techniki Budowlanej.
Obecnie prowadzone są kolejne badania systemów aero klejonych do papy i membrany. Najnowsze wyniki opublikowane zostaną na stronie www.energy5.pl.
Wykonane testy są podstawą do potwierdzenia zgodnie z przepisami deklarowanego poziomu właściwości użytkowych.
Właściwości użytkowe wyrobu budowlanego to dokument potwierdzający wprowadzenie wyrobu do obrotu. Dokument ten wydawany jest dla wyrobów, które przeszły badania na zgodność z normą lub posiadają Krajową albo Europejską Ocenę Techniczną. Dzięki określonym właściwościom wyrobów budowlanych, obiekty budowlane je posiadające lub z nich wykonane w całości, muszą spełniać tzw. podstawowe wymagania obejmujące:
- bezpieczeństwo konstrukcyjne,
- bezpieczeństwo pożarowe,
- bezpieczeństwo użytkowe,
- higienę, zdrowie, środowisko,
- ochronę przed hałasem,
- oszczędność energii, zachowanie ciepła.
Coraz częściej zdarza się, że Nadzór Inwestorski wymaga przedstawiania raportu badania TYPU. Każdy producent powinien więc posiadać własne badania potwierdzające w/w wymagania dotyczące wyrobu.
Wstępne badanie TYPU jest pełnym zestawem badań lub innych procedur opisanych w zharmonizowanych specyfikacjach technicznych, określającym właściwości użytkowe próbek wyrobu, reprezentatywnych dla danego typu. Typ wyrobu może obejmować wiele wersji wyrobu pod warunkiem, że różnice między wersjami nie mają wpływu na poziom bezpieczeństwa i inne właściwości wyrobu (określenie „typu” jest zazwyczaj podawane w normie lub ocenie technicznej, dotyczącej danego wyrobu).
Wstępne badanie typu pozwala na ocenę, czy wyrób jest zgodny z wymaganiami specyfikacji technicznej i, co istotne, pozwala na określenie poziomu deklarowanych właściwości wyrobu. Zakres wstępnego badania typu zależy od przewidywanych przez producenta zastosowań wyrobu i może ograniczyć się tylko do takich badań, które mają wpływ na zamierzone zastosowania. Jeżeli zastosowanie wyrobu jest zgodne z określonym w normie lub w ocenie technicznej, to badania typu obejmują wszystkie właściwości wyrobu.
Fot. nr 1. Testy wytrzymałościowe połączeń profili przeprowadzanych przez Instytut Techniki Budowlanej jako badania TYPU dla uzyskania Krajowej Oceny Technicznej.
Fot. nr 2. Testy wytrzymałościowe połączeń profili przeprowadzone przez Instytut Techniki Budowlanej jako badania TYPU dla uzyskania Krajowej oceny Technicznej.
Często spotyka się producentów podkonstrukcji, którzy posługują się badaniami w zakresie korozyjności, wykonanymi przez inny podmiot np. dostawcę materiału wsadowego nanoszącego powłokę antykorozyjną. W myśl powyższych wymogów, badaniom TYPU powinien być poddany cały oferowany zestaw (np. łączniki, styk różnych materiałów ze sobą, materiał głównej konstrukcji). W przeciwnym razie nie można zadeklarować tych parametrów dla oferowanego układu/zestawu. Na poniższym schemacie pokazano rolę badań TYPU / wstępnych badań TYPU, jakie powinny być wykonane, aby wyrób był dopuszczony do obrotu i stosowania zgodnie ze wskazanymi przepisami.
Kiedy mają zastosowanie Krajowe lub Europejskie Oceny Techniczne?
Krajowa Ocena Techniczna (KOT) stanowi jeden z rodzajów tzw. dokumentów odniesienia, pozwalających na wprowadzenie wyrobu budowlanego do obrotu. Dokumentami odniesienia są bowiem normy (zharmonizowane oraz Polskie Normy wyrobu), a także Oceny Techniczne (Europejskie oraz Krajowe). Producent przed wprowadzeniem wyrobu do obrotu zobowiązany jest dokonać oceny i weryfikacji stałości właściwości użytkowych z odpowiednim dokumentem odniesienia, tj. m.in. określić typ wyrobu i właściwości użytkowe zasadniczych charakterystyk wyrobu, które mają wpływ na spełnienie wymagań podstawowych przez obiekty budowlane, w których będą stosowane.
Z zapisów art. 5 ust. 2 oraz art. 9 ust. 1 ustawy z dnia 16 kwietnia 2004 r. o wyrobach budowlanych (Dz. U. z 2016 r., poz. 1570) wynika, że Krajowa Ocena Techniczna może być wydana wyłącznie dla wyrobu nieobjętego (lub nie w pełni objętego) normą zharmonizowaną oraz Polską
Normą wyrobu, a należącego do grup wyrobów z załącznika nr 1 do rozporządzenia Ministra Infrastruktury i Budownictwa z dnia 17 listopada 2016 r. w sprawie sposobu deklarowania właściwości użytkowych wyrobów budowlanych oraz sposobu znakowania ich znakiem budowlanym (Dz. U. z 2016 r., poz. 1966).
Przez wyrób nieobjęty lub nie w pełni objęty normą (zharmonizowaną albo Polską Normą wyrobu) należy rozumieć sytuacje opisane w art. 19 ust. 1 rozporządzenia Parlamentu Europejskiego i Rady (UE) nr 305/2011 oraz art. 9 ust. 1 ustawy o wyrobach budowlanych, z których wynika, że KOT (jak również ETA – Europejska Ocena Techniczna) mogą być wydane w sytuacjach, gdy:
- brak jest normy,
- gdy w odniesieniu do co najmniej jednej zasadniczej charakterystyki danego wyrobu (cechy wyrobu, którą producent będzie deklarował w odpowiedniej deklaracji właściwości użytkowych) metoda oceny przewidziana w normie nie jest właściwa,
- norma nie przewiduje żadnej metody oceny w odniesieniu do co najmniej jednej zasadniczej charakterystyki danego wyrobu.
Oznacza to m.in., że producent, który chce deklarować właściwości użytkowe wyrobu wykraczające poza zakres danej normy (np. PN -EN 1090), musi uzyskać odpowiednią (Europejską albo Krajową) Ocenę Techniczną, żeby wprowadzać wyrób do obrotu. Europejska Ocena Techniczna jest dokumentem wydawanym na wniosek producenta, jednak w przypadku jego braku dla wyrobu nieobjętego (albo nie w pełni objętego) zakresem normy, KOT jest jedynym dokumentem pozwalającym na wprowadzenie wyrobu do obrotu na polskim rynku. W związku z powyższym, aby zadeklarować dużo szerszy wachlarz właściwości użytkowych niż np. na normę PN-EN 1090, można zrobić to tylko i wyłącznie na podstawie Europejskiej lub Krajowej Oceny Technicznej. Takimi przykładami cech technicznych, których nie można zadeklarować na podstawie normy PN-EN 1090, a które są kluczowe z punktu widzenia bezpieczeństwa i trwałości użytkowania, są:
- badania wytrzymałościowe połączeń – np. osadzenia śrub młotkowych w kanałach profili aluminiowych lub stalowych,
- badania obciążenia paneli PV wraz z konstrukcją w zakresie oddziaływania wiatru i śniegu,
- siły, jakie przenoszą klemy montażowe środkowe i końcowe,
- odporność zestawu na uderzenie ciałem miękkim – ciężkim lub twardym – lekkim,
- odporność na uderzenie kamieniami.
Wyżej wymienione cechy techniczne spełniają niezwykle ważną rolę w bezpieczeństwie użytkowania wyrobu i jego trwałości, biorąc pod uwagę stabilność zamocowania lub próbę zniszczenia przez osoby postronne.
Konstrukcje wykonywane według normy PN-EN 1090-1
Aby producent wyrobu mógł wprowadzać produkt do obrotu i stosowania go w budownictwie na podstawie normy PN-EN 1090-1, na samym początku musi wykonać tzw. wstępne badania TYPU według punktu 6.2 przedmiotowej specyfikacji. Dodatkowo powinien wdrożyć Zakładową Kontrolę Produkcji (ZKP), ponieważ prefabrykacja konstrukcji według normy PN-EN 1090-1 odbywa się w zakładach, w których Zakładowa Kontrola Produkcji (ZKP) jest certyfikowana przez jednostkę notyfikowaną. Jednostka ta na podstawie wstępnej inspekcji i oceny oraz stałego nadzoru wydaje certyfikat zgodności ZKP.
Nie należy jednak łączyć i mylić tego certyfikatu z dokumentami, jakie wydawane są na zgodność z normą ISO 9001:2008. Certyfikat ZKP na zgodność z normą PN-EN 1090-1 jest wydawany tylko i wyłącznie w odniesieniu do systemu oceny zgodności 2+ i zawiera uprawnienia zakładu do produkcji wyrobów określonych klas wykonania (EXC 1, 2, 3, 4) oraz do sprecyzowanych metod deklarowania właściwości użytkowych. W samej jego treści powinniśmy przeczytać, na podstawie jakiej normy został wydany (PN-EN 1090-1), w jakim systemie oceny zgodności (2+), a także nazwę i adres producenta.
Wzór certyfikatu zawierający powołanie na normę PN-EN 1090 oraz klasę wykonania EXC.
Certyfikat musi zostać opatrzony nazwą jednostki, która go wydała, oraz jej uprawnieniami, czyli numerem notyfikacji. Dopiero uzyskanie takiego dokumentu i wykonanie wstępnych badań TYPU uprawnia producenta do wystawiania deklaracji właściwości użytkowanych i oznakowania wyrobu znakiem CE.
Nadzór inwestorski powinien również zwrócić uwagę, na jaką klasę wykonania konstrukcji według PN-EN 1090 został udzielony certyfikat w systemie oceny zgodności 2+. Norma PN-EN 1090 „Wykonanie konstrukcji stalowych i aluminiowych” wprowadza pojęcie klasy wykonania konstrukcji EXC. Opierając się na wytycznych zawartych we Wzorcowej Liście Zarządzeń Technicznych otrzymujemy wytyczne do przyporządkowania budowli do poszczególnych klas wykonania:
- Klasa wykonania EXC1 – do tej klasy wykonania zalicza się elementy konstrukcyjne lub konstrukcje nośne, poddane obciążeniom przeważająco stałym, wykonane ze stali o klasie wytrzymałości do 275MPa.
- Klasa wykonania EXC2 – do tej klasy wykonania zalicza się elementy konstrukcyjne lub konstrukcje nośne, poddane obciążeniom przeważająco stałym i nieprzeważająco stałym (dynamicznym), wykonane ze stali do klasy wytrzymałości S700, które nie powinny być przyporządkowane klasom wykonania EXC1, EXC3, EXC4.
- Klasa wykonania EXC3 – do tej klasy wykonania zalicza się elementy konstrukcyjne lub konstrukcje nośne poddane obciążeniom przeważająco stałym i nieprzeważająco stałym (dynamicznym), wykonane ze stali do klasy wytrzymałości S700.
- Klasa wykonania EXC4 – do tej klasy wykonania zalicza się wszystkie elementy konstrukcyjne lub konstrukcje nośne klasy o ekstremalnych w skutkach awarii dla ludzi i środowiska.
W związku z powyższym certyfikat w systemie oceny zgodności 2+ na normę PN-EN 1090 określa, w jakich klasach dany producent może wykonywać konstrukcję oraz z jakiego materiału. Często bowiem zdarza się tak, że dany producent wykonuje konstrukcję z materiału np. GD 350, a posługuje się certyfikatem, który określa klasę wykonania EXC1 (czyli może używać stali o klasie wytrzymałości do 275MPa).
Normy jakościowe serii ISO 9001
Normy jakościowe serii ISO 9001 są narzędziem przydatnym w uporządkowaniu działań np. procesów produkcyjno-realizacyjnych firmy i nie są to dokumenty obligatoryjne do stosowania. Tymczasem większość producentów, w tym zagranicznych, legitymuje się certyfikatami w tym zakresie, nie spełniając jednocześnie wymogów prawnych wynikających z ustawy o wyrobach budowlanych. Podkreśla się, że wprowadzanie wyrobów do obrotu i stosowania niezgodnie z ustawą o wyrobach budowlanych, podlega interwencji Powiatowego i Głównego Inspektora Nadzoru Budowlanego. Wymienione instytucje nadzoru w trybie art. 13, 14 Ustawy o Wyrobach Budowlanych rozpoczynają procedurę sprawdzenia wyrobów, a w przypadku używania niezgodnie znaku CE odbywa się to wraz z raportowaniem do Prezesa UOKiK. Wyroby wprowadzone do obrotu niezgodnie z przepisami w trybie art. 15 wyżej wymienionej ustawy trafiają na listę wyrobów niezgodnych i zostają wycofane z obrotu.
Innym bardzo ważnym aspektem budowy naziemnych i dachowych instalacji fotowoltaicznych jest dobór odpowiedniego zabezpieczenia antykorozyjnego w zależności od użytego materiału. Często spotyka się konstrukcje stalowe z powłoką Z275 wg PN-EN 10346, którą nanosi się na blachy i taśmy o grubości do 2,5 mm. Naniesienie powłoki cynkowej następuje w hucie przez zanurzenie blachy w kąpieli z roztopionego metalu zawierającej co najmniej 99 proc. cynku. Większość wyrobów wykonywanych jest powłoką o typowej grubości 20μm (od 15μm do 27μm). Zgodnie z normami, blachy z tego typu zabezpieczeniem antykorozyjnym nie nadają się do stosowania na zewnętrz. Są dedykowane tylko do pomieszczeń o kategorii korozyjności C2 – budynków nieogrzewanych, w których może mieć miejsce kondensacja pary wodnej, np. magazyny, hale sportowe.
Natomiast konstrukcje pod moduły fotowoltaiczne powinny spełniać wymagania dla kategorii korozyjnej środowiska min. C3 – chodzi o środowiska miejskie i przemysłowe, charakteryzujące się średnim zanieczyszczeniem tlenkiem siarki (IV), obszary przybrzeżne o małym zasoleniu, C4 to obszary przemysłowe i obszary przybrzeżne o średnim zasoleniu lub C5-I – obszary przemysłowe o dużej wilgotności i agresywnej atmosferze.
Dodatkowo zawraca się uwagę na fakt, że norma PN-EN 12944-2:2001 precyzuje ubytki powłoki cynkowej w zależności od kategorii korozyjnej środowiska. I tak przy kategorii korozyjnej C3 może to być nawet 2,1 µ/rok dla konstrukcji nad ziemią bez elementów wbijanych. Oznacza to, że elementy wykonane w tym przypadku z blachy cynkowanych Z275 o najcieńszej z możliwych grubości (15 µ) już po około 7 latach mogą stracić całkowicie powłokę antykorozyjną.
Natomiast w przypadku kategorii korozyjnej C4 degradacja powłoki może nastąpić już po około 3,5 roku. Najgorzej wygląda to w przypadku środowiska korozyjnego C5-I, gdzie powłoka Z275 może być zniszczona w przeciągu około 2 lat – stąd też obostrzenia co do możliwości zastosowań powłoki Z275.
Kategorie korozyjności atmosfery i przykłady typowych środowisk zgodnie z normą PN-EN ISO 12944-2:2001.
Podobnie sytuacja wygląda w przypadku wyrobów stalowych, zabezpieczanych cynkowaniem zanurzeniowym według PN-EN ISO 1461. W tym zakresie wyroby wykonane ze stali „czarnej” po zakończeniu procesu produkcyjnego są zanurzane w roztopionym cynku o temp. 4500C. Zgodnie z PN-EN ISO 1461 grubość miejscowa powłoki cynku (minimalna wartość) wynosi:
- 45µ dla materiału o grubości do 1,5 mm,
- 55µ dla materiału o grubości od 1,5 do 3 mm,
- 70µ dla materiału o grubości od 3 do 6 mm.
Wyroby z powłoką cynkową nanoszoną metodą zanurzeniową nadają się do środowisk z kategorią korozyjności C3 oraz z pewnymi ograniczeniami C4 (np. zakłady spożywcze, pralnie, browary, mleczarnie). W pomieszczeniach o kategorii korozyjności C4 i C5 mogą być zastosowane wyroby ocynkowane, a następnie pomalowane farbami epoksydowymi (z naciskiem na pomieszczenia).
W przypadku mocowań opierających się na profilach aluminiowych należy zwrócić uwagę na rodzaje stopów aluminium i ich klasyfikacji trwałości w zależności od środowiskach wg normy EN 1999-1-1:2007+A1:2009. W normie tej mamy wymienione klasy trwałości A, B i C przyporządkowane do sposobu ochrony od warunków eksploatacji oraz grubości materiału. Może bowiem okazać się, że np. w środowisku przemysłowym, wiejskim lub ciężkim zastosowany stop aluminium klasy trwałości B i w zależności od jego kształtu i budowy będzie musiał być dodatkowo zabezpieczony antykorozyjnie.
W doborze rozwiązań mocowań często pomijany jest aspekt poprawnego doboru elementów złącznych. Zaleca się głównie wyroby ze stali nierdzewnych, które są sklasyfikowane w normach PN-EN ISO 3506, oraz gatunki stali nierdzewnych odpornych na korozję, które są objęte normami PN-EN 10088-1-5. Na podstawie wymienionych norm i charakterystycznych własności stali nierdzewnych opracowano poniższą tablicę, w której podano zalecane gatunki stali nierdzewnych w zależności od korozyjności atmosfery eksploatacji.
Zalecane gatunki stali nierdzewnych w zależności od korozyjności atmosfery eksploatacji.
Stale nierdzewne w omawianym środowisku korozyjnym nie wymagają zastosowania dodatkowych powłok ochronnych. Dla uzyskania maksymalnego czasu bezawaryjnej eksploatacji konieczny jest prawidłowy dobór materiału pod względem odporności korozyjnej, o której w tym przypadku decyduje odporność na korozję wżerową i szczelinową, związaną ze stężeniem pierwiastków stopowych molibdenu i chromu.
Instalacje fotowoltaiczne, w zależności od miejsca wbudowania, rodzaju konstrukcji i sposobu montażu, są wykonywane z różnych materiałów. Należy wówczas przestrzegać kilku najważniejszych zasad. Głównie w instalacjach dachowych, ale również naziemnych, stosuje się elementy profili aluminiowych skręcanych ze sobą w sposób mechaniczny i niejednokrotnie obudowanych blachami. W tym zakresie zakazane jest używanie jakichkolwiek elementów wykonanych ze stali czarnej ocynkowanej, które bezpośrednio stykają się z aluminium.
W przypadku blach należy odizolować dwie powierzchnie (stal ocynkowana i aluminium) przekładkami z folii lub taśm, natomiast w przypadku wkrętów i śrub do aluminium można stosować tylko wykonane ze stali nierdzewnej o klasie A2 lub A4. W przeciwnym razie już po kilku miesiącach zauważymy powstające ognisko korozji w miejscu zastosowania np. wkrętu ocynkowanego.
Często spotyka się również zastosowanie kotew ocynkowanych mocujących instalację do budynku poprzez aluminiowe marki/konsole. W takim przypadku zachodzą dwie niezgodności – pierwsza to korozja międzymateriałowa na styku kotwy z konsolą/marką montażową. Druga zaś dotyczy stosowania kotew w odmianie ocynkowanej na zewnątrz budynku. Ze względu na warstwę ochrony korozyjnej (ocynk), tego typu elementy są przeznaczone do stosowania tylko i wyłącznie wewnątrz budynków w pomieszczeniach suchych.
Biorąc pod uwagę powyższe, mocowania wraz z wkrętami używane w kontakcie z aluminium powinny być zawsze wykonywane łącznikami nierdzewnymi. Aluminium w stosunku do stali nierdzewnej jest anodą, a stal nierdzewna katodą.
W związku z tym połączenie aluminium i stali nierdzewnej teoretycznie mogłoby powodować powstawanie różnicy potencjałów, co w konsekwencji może być przyczyną występowania zmian korozyjnych. Należy jednak pamiętać, że odstępstwem od tej reguły są przypadki połączeń metali o znacznej różnicy potencjałów, gdzie ważnym czynnikiem jest stosunek powierzchni anody do katody.
Duża powierzchnia katody (stali nierdzewnej) w stosunku do małej powierzchni anody (aluminium) przyspiesza proces korozji, natomiast odwrotny przypadek w skuteczny sposób to eliminuje. Specyficzna budowa podkonstrukcji pod moduły fotowoltaiczne charakteryzuje się dużą powierzchnią profili aluminiowych w stosunku do występujących punktowo łączników nierdzewnych. W tych konkretnych rozwiązaniach różnica wielkości potencjału stopu aluminium w stosunku do stali nierdzewnej jest dużo mniejsza, a tym samym nie zachodzi zagrożenie korozyjne. Dodatkowo należy nadmienić, że łączniki nierdzewne w konstrukcjach aluminiowych nie rdzewieją, ponieważ podatność metali i stopów na korozję elektrochemiczną jest zależna od składu chemicznego i struktury fazowej stopu.
Odpowiedni dobór składu chemicznego powoduje przesunięcie standardowego potencjału elektrodowego do wartości dodatnich, zapewniając wysoką odporność na korozję. Działanie takie w przypadku stali nierdzewnych zapewnia dodatek ok. 18% chromu. Dodatki innych składników stopowych, takich jak mangan, nikiel, miedź, powodują uodpornienie się stali na bardziej agresywne działanie środowiska korozyjnego (np. kwasów, zasad). To dodatek chromu, pozwalający na wytworzenie warstwy pasywnej, zapewnia dostateczną ochronę przed korozją.
To właśnie warstwy pasywne są odpowiedzialne za brak reakcji stali nierdzewnej i aluminium, gdyż posiadają zbliżony potencjał elektryczny. Kontakt tych warstw przy połączeniu nie wywołuje zjawiska korozji elektrochemicznej. Uszkodzone podczas montażu warstwy pasywne w krótkim czasie ulegają regeneracji, zapewniając odpowiednie właściwości ochronne.
Warstwa pasywna zapobiega też korozji w przypadku kontaktu stali nierdzewnej z alkalicznymi materiałami budowlanymi, takimi jak beton, zaprawy itp., czego z kolei nie można stwierdzić w przypadku elementów wykonanych z aluminium. W takich przypadkach należy zawsze stosować przekładki odizolowujące obydwa materiały, w tym przypadku są to beton i aluminiowa konsola.
Podsumowując, każdy producent podkonstrukcji powinien legitymować się badaniami i dokumentami odniesienia dla zestawu wyrobów, które jednoznacznie potwierdzą wszystkie cechy wyrobu. Obecnie na rynku spotykamy się z praktykami, które polegają na kupowaniu/kompletowaniu elementów podkonstrukcji od wielu dostawców – niestety nigdy nie były one przebadane razem jako zestaw wyrobów (tym samym nie mogą być one dopuszczone do obrotu i stosowania w budownictwie).
Innym aspektem jest, że to inwestor powinien porównać zadeklarowane cechy techniczne wyrobu pod kątem bezpieczeństwa użytkowania oraz trwałości, co bezpośrednio przekłada się na dokumenty odniesienia (Krajowe Oceny Techniczne lub normy zharmonizowane PN-EN 1090-1).
Materiały źródłowe:
- Rozporządzenia Parlamentu Europejskiego i Rady (UE) nr 305/2011.
- Ustawy z dnia 16 kwietnia 2004 r. o wyrobach budowlanych (Dz. U. z 2016 r., poz. 1570)
- Norma PN-EN 1090-1 Wykonanie konstrukcji stalowych i aluminiowych — Część 1: Zasady oceny zgodności elementów konstrukcyjnych.
- Krajowa Ocena Techniczna ITB-KOT-2018/0109
- Materiały techniczne firmy ENERGY5 sp. z o.o.- www.energy5.pl
artykuł sponsorowany